Ausgangssituation
In Branchen, die strenge Qualitätsstandards einhalten müssen, ist präzise und effiziente Produktion von Kunststoffteilen im Spritzgussverfahren von zentraler Bedeutung. Traditionelle Verfahren zur Bestimmung optimaler Prozessparameter stützen sich oft auf einen zeitaufwändigen und kostspieligen Versuch-und-Irrtum-Ansatz. Angesichts wachsender Anforderungen an die Produktqualität und der Notwendigkeit, Produktionsfehler zu verringern, ist es daher entscheidend, moderne datenbasierte Methoden zu entwickeln. Diese sollten sowohl die präzise Vorhersage der Produktqualität als auch die optimale Bestimmung der Spritzgussparameter ermöglichen, um die Effizienz des Produktionsprozesses zu steigern.
Herausforderung
Eine der Herausforderungen im Spritzgussverfahren besteht darin, die Vielzahl an Prozessparametern wie Temperatur, Druck und Abkühlzeit etc. so zu steuern, dass das Endprodukt den hohen Qualitätsstandards entspricht. Diese Parameter sind oft eng miteinander verknüpft und können durch äußere Faktoren wie Umgebungsbedingungen zusätzlich beeinflusst werden. Die nicht linearen Zusammenhänge zwischen den Prozessparametern und der Produktqualität machen die Optimierung zu einer komplexen Aufgabe, die mit herkömmlichen Methoden schwer zu bewältigen ist. Daher ist es entscheidend, eine Lösung zu finden, die diese Komplexität effektiv meistert und gleichzeitig eine hohe Produktqualität sicherstellt.
Vorgehen
Im Rahmen des Umsetzungsprojekts mit der Plastic Concept GmbH haben unsere KI-Experten einen datengetriebenen Ansatz zur Prozessoptimierung analysiert, der maschinelles Lernen mit Optimierungsalgorithmen kombiniert. Sie haben zunächst ein Prozessmodell trainiert, das die Beziehung zwischen verschiedenen Prozessparametern und der Produktqualität anhand vorhandener Daten abbildet und die Qualität der gefertigten Teile vorhersagt. Anschließend haben sie einen genetischen Algorithmus eingesetzt, um die optimalen Parameterkombinationen für eine fehlerfreie Produktion zu ermitteln, unter Berücksichtigung aller Restriktionen. Sollte eine Parameterkombination zu schlechterer Qualität führen, kann die KI dies frühzeitig vorhersagen und sofort neue Konfigurationen vorschlagen, die mögliche negative Einflüsse ausgleichen und eine konstant hohe Qualität sichern.
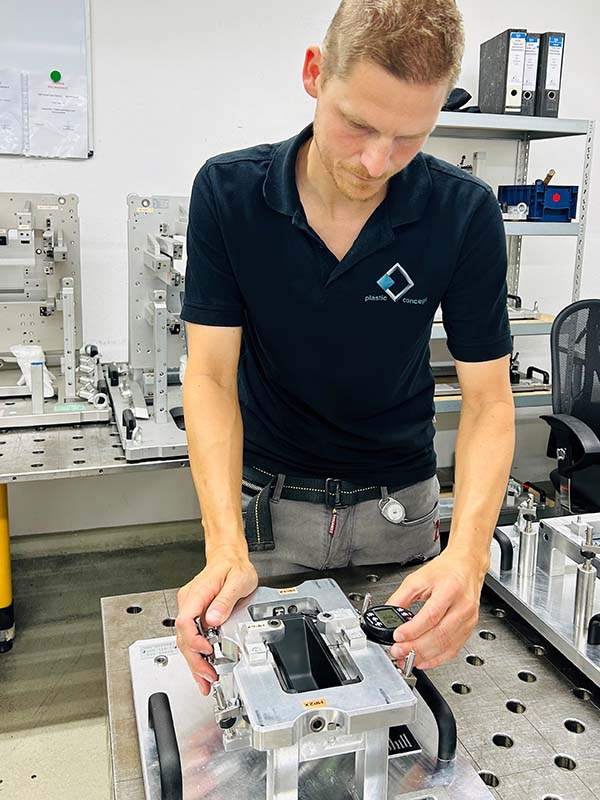
Lösung
Die Analyse zeigte, dass datengetriebene Methoden in der Lage sind, die Qualität der Teile mit hoher Genauigkeit zu prognostizieren und die Prozessparameter effizient zu optimieren. So können Fehler reduziert und eine hohe Produktqualität erreicht werden. Diese Vorgehensweise ist nicht nur auf das Spritzgussverfahren beschränkt, sondern kann auch in anderen Anwendungsbereichen eingesetzt werden. Voraussetzung für den Erfolg der vorgeschlagenen Methode sind ausreichend qualitativ hochwertige Daten, die verschiedene Zusammenhänge abbilden und den gesamten Prozess widerspiegeln.
Unsere Zusammenarbeit in diesem spannenden Projekt zeigt, wie die Implementierung von KI im Kunststoffspritzguss entscheidend zur Minimierung von Ausschuss und zur Schonung von Ressourcen beitragen könnte. Das große Potenzial der Initiative Mittelstand-Digital eröffnet zukünftig neue Möglichkeiten, um Effektivität als Weg zu nachhaltigen Prozessen zu fördern.