Ausgangssituation
Künstliche Intelligenz spielt eine immer größere Rolle bei der Automatisierung und Optimierung von verschiedensten Produktionsprozessen, wie zum Beispiel der Zerspanung. Vor diesem Hintergrund untersucht das Fraunhofer-Institut IWU in einem hausinternen Forschungsprojekt, wie Verfahren der Künstlichen Intelligenz zur Überwachung und Verbesserung von Bohrprozessen eingesetzt werden können. Denn aufgrund der schweren Zugänglichkeit von Bohrlöchern ist eine direkte Überprüfung des Bohrergebnisses durch optische oder andere Prüfverfahren häufig schwer bis unmöglich. Hier bieten datenbasierte Prognosemodelle der künstlichen Intelligenz eine Möglichkeit der Qualitätsüberprüfung ohne invasive Eingriffe. Material- und Fehlererkennung sowie Zustandsüberwachung von Werkzeug und Maschine sind weitere Beispiele für Lernaufgaben, welche sich aus Bohrprozessen ableiten. Sie können mit den unterschiedlichen Herangehensweisen und Algorithmen der künstlichen Intelligenz gelöst werden.
Herausforderung
Um Prognosemodelle trainieren zu können, benötigt man eine ausreichend große Datenbasis. Sie muss einerseits qualitative Anforderungen, wie z. B. Genauigkeit, Vollständigkeit, Konsistenz und Aktualität, erfüllen und andererseits für das zu lösende Problem repräsentativ sein. Während moderne Maschinen üblicherweise von vornherein über eine digitale Datenerfassung verfügen, müssen ältere Anlagen zunächst mit Sensorik und weiterer Software zum Datenmanagement ausgestattet werden (Retrofitting). Eine weitere Hürde stellt die Übertragbarkeit der angelernten Modelle auf neue Maschinen, Werkzeug oder Prozessumgebungen dar. Ebenfalls ist die Interpretierbarkeit moderner Verfahren der künstlichen Intelligenz herausfordernd.
Vorgehen
Um prozessbegleitend Einschätzungen über Eigenschaften des Bohrmaterials oder die Oberflächenqualität von Bohrungen zu erhalten, können verschiedene Sensoren an der Bohrmaschine oder in Prozessnähe sowie ebenfalls Strom- und Spannungsmessungen zum Einsatz kommen. Üblicherweise werden hier Schall- und Beschleunigungsmesser verwendet. Die aus den Sensorsignalen entstehenden Zeitreihendaten werden zunächst einigen Vorverarbeitungsschritten unterzogen. Dazu zählt beispielsweise die Berechnung der zugrunde liegenden Frequenzen im Signal, welche bei Bohrprozessen sehr aussagekräftig sind. Die entstandenen Trainingsdaten werden dazu genutzt, Prognosemodelle zu erlernen, zu testen und in Hinblick auf Genauigkeit und Laufzeit zu prüfen. Je nachdem, welches Problem aus der Bohrpraxis bearbeitet werden soll, können Datenwissenschaftler:innen entscheiden, welches Vorgehen der Modellierung und welche Algorithmen für die Lösung geeignet sind.
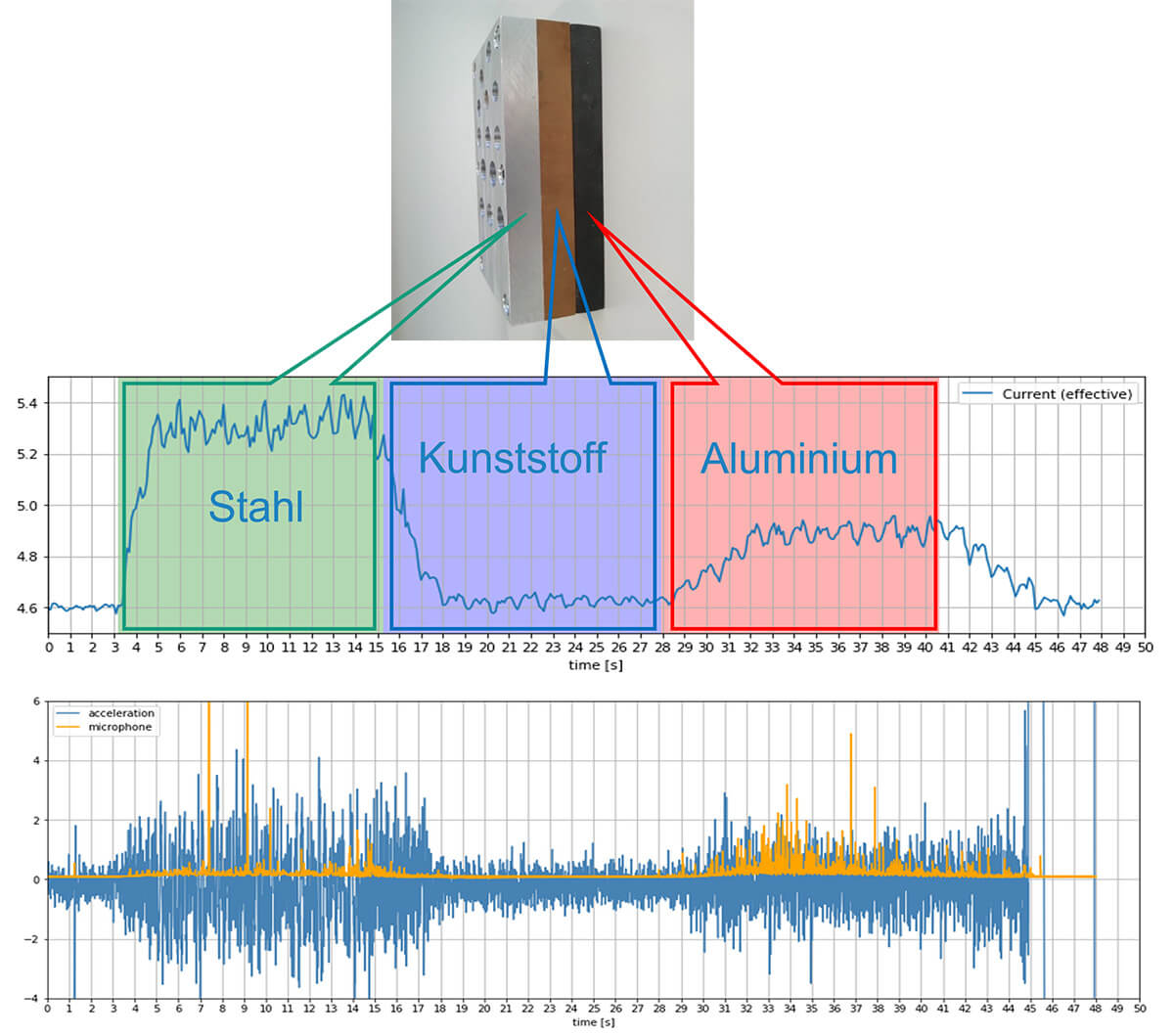
Lösung
Mit einem erfolgreich trainierten und geeigneten Modell sowie einer ansprechenden Visualisierung der Prognose können Bohrprozesse automatisch überwacht werden. Somit unterstützen sie den Menschen an der Maschine. Um die Vorhersage darüber hinaus für die Verbesserung des Bohrprozesses zu nutzen, wird das Prognosemodell mit einem Optimierungsalgorithmus gekoppelt. Die daraus resultierende adaptive Prozessregulation ist die Voraussetzung für eine Verbesserung der Ressourceneffizienz beim Bohren in Hinsicht auf Material und Energie. Da bei der Modellgenerierung insbesondere Frequenzeigenschaften und statistische Kennzahlen der Prozessdaten von Bedeutung sind, können mithilfe von künstlicher Intelligenz außerdem wertvolle Rückschlüsse und Erkenntnisse auf den Bohrprozess an sich gezogen werden.