Ausgangssituation
Die Norafin Industries (Germany) GmbH produziert wasserstrahlverfestigte und vernadelte Spezialvliesstoffe und Composites. Am Standort in Mildenau sind circa 200 Mitarbeitende beschäftigt. Das Unternehmen beliefert zum Beispiel die Kosmetikbranche, die Baubranche oder die Spezialreinigungsbranche mit Vliesstoffen. Norafin kann dabei auf individuelle Kundenwünsche eingehen und eine Produktpalette mit über 400 Produkten zur Verfügung stellen. Dadurch stellte sich ein Optimierungs- und Digitalisierungsbedarf für die Lagerlogistik heraus, dem das Unternehmen gemeinsam mit dem Mittelstand-Digital Zentrum Chemnitz nachging.
Die Lager- und Logistikprozesse bei Norafin sind historisch gewachsen und haben sich als Routinen verfestigt. Da es keine klare Prozessstruktur für das Lagern der fertigen Produkte gibt, ist die Lagerfläche häufig überfüllt und die Produkte müssen an anderen Orten zwischengelagert werden. Das führt zu Prozessverschwendung in Form von Intransparenzen und einem hohen Suchaufwand. Die hohe Produktvielfalt und die dazugehörige Datenvielfalt erschweren eine klare Kategorisierung und Zuordnung.
Die Einsicht ist da, dass wir bessere Strukturen brauchen. Auch der Wille ist da und auf jeden Fall auch die Unterstützung der Geschäftsleitung.
Vorgehen
Im ersten Schritt analysierte das Team den internen Materialfluss und die Logistikflächen. Es erarbeitete auf Basis mehrerer Workshops und Datenanalysen einen Soll-Ist-Vergleich der vorhandenen und notwendigen Lagerflächen. Mittels des Lagerplans konnten die Flächen digital abgebildet und Materialflüsse eingearbeitet werden. So ist eine genaue Analyse möglich, wie häufig, in welchen Mengen und zu welchen Maschinen Material oder Produkte transportiert werden. Ziel war es, die Grundlagen für datenbasierte Entscheidungen zu schaffen.
Anschließend entwickelten die Experten aus dem Digitalzentrum Chemnitz gemeinsam mit Norafin die Anforderungen für mögliche Lagersysteme und für eine staplerlosen Logistik. Besuche bei mehreren Unternehmen mit unterschiedlichen Lösungen verdeutlichten den Nutzen und die Anwendung eines fahrerlosen Transportsystems (FTS).
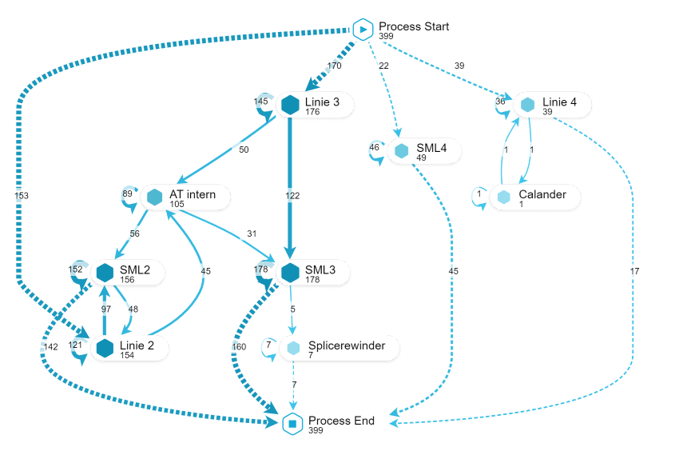
Begleitend dazu nahmen vor allem die Abteilungen Produktion, Lager und Logistik alle Arbeitsschritte strukturiert auf – zum einen durch Beobachtungen vor Ort und zum anderen durch Gespräche mit Mitarbeitenden und Produktionsleitenden. Dadurch konnten die Lager- und Logistikprozesse nach Vorgaben der Spezifikationssprache BPMN (Business Process Model and Notation) und mit Hilfe von Visio als Prozessmodell visualisiert werden.
All das, was wir subjektiv die letzten Jahre gesagt haben, ist jetzt wirklich mit Zahlen belegt. Das ist eine gute Basis für Prozesse, die aus meiner Sicht das Wichtigste sind.
Lösung
Auf Grundlage der Soll-Ist-Entwicklungen wurden drei Typenvertreter, die circa 90 Prozent der Produkte bei Norafin abdecken, herausgearbeitet. Diese spiegeln unterschiedliche Aspekte des Produktionsprogrammes wider – große Produktionsvolumina, hohe Logistikaufwände oder auch hohe Fertigungsumfänge. Mittels dieser Typenvertreter und der zugehörigen Fertigungsfolgen konnten die Buchungsreihen strukturierter analysiert und beispielsweise die Lagerkapazitäten digital dargestellt werden.
Die Kombination des fabrikplanerischen Ansatzes mit der Process-Mining-Methode half, die Ursachen für die stark schwankenden Flächenbedarfe und damit einhergehenden unterschiedlichen Transportkapazitäten zu identifizieren. Das Team stellte fest, dass die Varianz der Produkte, und deren Prozessumfänge zu erhöhten Anforderungen an Lagerflächen und -zeiten führen.
Das Projekt fokussierte die Lösungssuche auf die Optimierung des Transports, vorrangig mit Staplern. Hierfür wurden die Transporte eines Quartals als Basis genommen, um die zugehörigen Transportzeiten (ca. 150 Stunden) zu ermitteln. Zur Plausibilisierung erfolgte ein Abgleich mit den Nutzungsdaten der Betriebsmittel. Dabei sind etwaige Suchaufwände nach Paletten, die Suche und Bereitstellung von Staplern, Leerfahrten oder weitere Nebentätigkeiten nicht inbegriffen. Der reale Zeitaufwand für die Mitarbeitenden kann als drei Mal höher eingeschätzt werden (ca. 450 Stunden). Durch die Integration automatisierter Fördertechnik wie eines FTS können Transportaufwände und somit Kosten gespart werden. Es soll an bereits vorhandene Fördertechnik angebunden und somit die Zusammenarbeit zwischen der Produktion und dem Endproduktelager verbessern.