Ausgangssituation
Verzahnungen für die Automobilindustrie erfordern eine hohe Oberflächengüte. Dies kann durch die Feinbearbeitung erreicht werden. Hier zeichnet sich das sogenannte kontinuierliche Wälzschleifen als ein Fertigungsprozess mit enormer Produktivität und hoher Genauigkeit aus. Um die Schleifqualität aufrecht zu erhalten, ist ein regelmäßiges Abrichten erforderlich, welches in einer Folge von Abrichthüben vollzogen wird. Um möglichst produktiv zu fertigen und das Werkzeug so lange wie möglich nutzen zu können, sollten nicht mehr Abrichthübe als nötig durchgeführt werden. Aufgrund mangelnder Möglichkeiten, den Abrichtprozess zu überwachen, wird die Anzahl der Hübe allerdings in der Regel fix vom Maschinenbedienenden festgelegt und beinhaltet eine große Sicherheit. Um das Potential des Schleifwerkzeuges voll auszunutzen, wäre die automatisierte Erkennung eines ausreichend abgerichteten Werkzeugs nötig. Hier kann künstliche Intelligenz unterstützen. Methoden des Maschinellen Lernens (ML) bieten die Möglichkeit, ein abgerichtetes Werkzeug auf Grundlage der Sensordaten zu detektieren.
Herausforderung
Moderne Wälzschleifanlagen sind bereits mit verschiedenen Sensorsystemen ausgestattet. Acoustic Emission (AE) – Sensoren liefern zeitlich hoch aufgelöste Informationen beim Abrichten. Diese hohe Auflösung beschränkt jedoch die Möglichkeit, die Informationen durch klassische Methoden der Signalverarbeitung vollumfänglich auszuwerten. Gleichzeitig muss die Auswertung unabhängig von der Amplitude des Signals erfolgen, da die Methode sonst durch die Positionierung der Sensorik und Größe des Schleifwerkzeugs beschränkt wäre.
Vorgehen
Um ein Machine Learning Modell für die Klassifikation des Werkzeugzustandes zu trainieren, wurde ein Schleifwerkzeug in mehreren Versuchen verschlissen und anschließend abgerichtet. Für die Beurteilung, ob das Werkzeug ausreichend abgerichtet wurde, erfolgte die Fertigung von Testwerkstücken nach dem Abrichten. Die insgesamt sechs damit erzeugten Abrichtzyklen reichen jedoch bei Weitem nicht aus, um Methoden des Maschinellen Lernens einzusetzen. Deshalb wurde der Datensatz so umstrukturiert, dass die Klassifikation nicht für komplette Abrichthübe, sondern für einzelne Datensequenzen (Snippets) erfolgt. Diese Snippets entsprechen einzelnen Abschnitten des Werkzeugs. Um die Vorhersagen unabhängig von der Amplitude des Signals zu gestalten, werden alle Snippets in einem Vorverarbeitungsschritt normiert. Als Modell wurde ein Residual Neural Network genutzt und auf die Struktur der Daten zugeschnitten. Die Modellparameter, wie beispielsweise die Anzahl der Schichten im Netzwerk oder die Anzahl der Filter wurden mittels Hyperparameter Optimierung ausgewählt. Die erreichte Genauigkeit auf dem vom Training ausgeschlossenen Testdatensatz Betrug 95 Prozent.
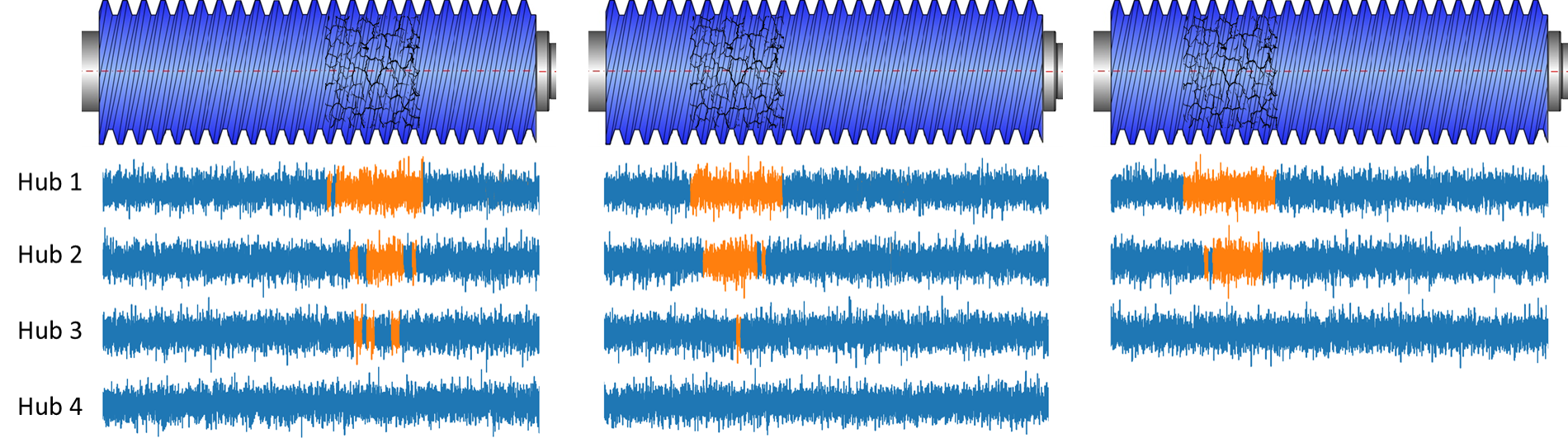
Abbildung 1: Drei verschiedene Serien von Abrichthüben. Das AE-Signal ist orange dargestellt, wenn das Modell den Bereich als „verschlissen“ klassifiziert und blau eingefärbt, wenn der Bereich durch das Modell als „nicht verschlissen“ eingestuft wird.
Lösung
Mit dem trainierten Machine Learning Modell zur Klassifizierung von Datensequenzen beim Abrichten ist der Grundstein für einen optimierten Abrichtzyklus gelegt. Die Automatisierte Detektion des erfolgreich abgerichteten Werkzeuges ermöglicht eine längere Werkzeugstandzeit und kürzere Unterbrechungen des Fertigungsprozesses. Das Machine Learning Modell stützt sich dabei auf die vorhandene Acoustic-Emission-Sensorik der Maschine. Durch die geschickte Umstrukturierung der Trainingsdaten konnte das ML-Modell bereits mit Daten von lediglich sechs Abrichtzyklen trainiert werden und erreichte bereits eine hohe Genauigkeit. Außerdem ist die Lösung unabhängig von der Amplitude des Signals einsetzbar, da alle Datensequenzen vor der Klassifizierung normiert werden.