In dieser Ausgabe der Nachgelesen-Reihe erfahren Sie:
- Was Retrofit ist,
- welchen Nutzen Retrofit für Unternehmen bietet und
- mit welchen Technologien Retrofit beispielhaft umgesetzt werden kann.
Retrofit im Kontext von Industrie 4.0
Die vierte industrielle Revolution (Industrie 4.0) schreitet kontinuierlich voran. Technologische Innovationen führen zu einer Vernetzung von Mensch, Maschine und Werkzeug. Eine Steigerung der Flexibilität, eine Optimierung von Produktionsabläufen und neue Marktchancen sind nur einige der Vorteile, die die vierte industrielle Revolution ermöglicht.
Zur Umsetzung von Industrie 4.0 muss jedoch nicht der komplette Maschinenpark ersetzt werden, sondern kann durch Retrofit, also der Modernisierung von Bestandsanlagen, Industrie-4.0-fähig gemacht werden. Der Begriff „Retrofit“ leitet sich von den Wörtern „retro“ für rückwärts und „to fit“ für anpassen ab. Das heißt durch die Auf- bzw. Nachrüstung von vorhandenen Maschinen können diese „smart“ gemacht und in übergeordnete Systeme, wie Manufacturing Execution System (MES) oder Enterprise-Resource-Planning (ERP), eingebunden werden.
Während mechanische Bauteile langlebiger sind, haben Software und Steuerungstechnik einen kürzeren Lebenszyklus. Deshalb ist im Vergleich zu einer Neuanschaffung der Retrofit einer bestehenden Anlage wesentlich kostengünstiger.
Gründe für Retrofit
- Möglichkeit zur Erfassung von noch nicht vorhandenen Maschinen- und Prozessdaten zur
- Steigerung der Energieeffizienz,
- Erhöhung der Produktqualität und
- Prozessverbesserung
- Nutzungsdauer von Bestandsanlagen verlängern; Maschinenbestand auf den aktuellen technischen Stand bringen
- Verringerung von Ausfallzeiten; Maschinenzustände überwachen und damit eine vorausschauende Instandhaltung ermöglichen
Voraussetzungen
- Definieren der Einflussgrößen: Welche Maschinenparameter sind für die Produktqualität relevant (z. B. Temperatur)?
- Auswahl geeigneter Sensoren: Wie können physikalische Messgrößen aufgenommen werden? Welche Umgebungsbedingungen herrschen vor? Welche konstruktiven Einschränkungen sind zu beachten (z. B. berühungsloses Messen der Temperatur, genügend Bauraum für eine Kraftmessdose an relevanter Stelle)?
- Auswahl der Kommunikationsschnittstelle/des IoT-Gateways (Internet der Dinge-Gateway – Gerät zur Befähigung von Interoperabilität): Unterstützung welcher Kommunikationsprotokolle?
- Einbindung der Daten an übergeordnete Systeme: Wie sollen die Daten ausgewertet werden?
Technologische Komponenten
In welchem Umfang und mit welchen Technologien eine Nachrüstung von Maschinen möglich ist, hängt vom Anwendungsfall und vom Zustand der jeweiligen Anlagen ab.[1] Auf dem Markt haben sich diverse Anbieter etabliert, die unterschiedliche Lösungen anbieten. Die folgenden stellen nur eine Auswahl dar und bieten einen Überblick.
Auswahl von Anbietern (in alphabetischer Reihenfolge):
- Bosch Rexroth – IoT Gateway (sehr umfangreiches Paket): Diese Lösungen bieten Hardware, Software und ein Device Portal als Cloud an. Hier können verschiedene Sensoren angebracht und Zustände über die Cloud standortübergreifend überwacht werden.
- Inhub – eSYS: Dieses Produkt ermöglicht die Erfassung und Auswertung von Strommustern ohne Eingriffe in die Maschine.
- Pepperl+Fuchs – SmartBridge: Dieses Produkt kann Daten einer IO-Link (Kommunikationssystem zur Anbindung von Sensoren/Aktoren) Kommunikation anzeigen oder als Master-Modul zusätzlich zur Datenanzeige auch die Parametrierung von IO-Link-fähigen Sensoren und Aktoren unterstützen.
- SKF – QuickCollect: Dieses Produkt ist ein mobiler Sensor, der die Daten (Schwingungsgeschwindigkeit, Geschwindigkeit, Hüllkurvenbeschleunigung und Temperatur) per Bluetooth an Apps (iOS/Android) oder in die Cloud übermittelt. Durch die kompakten Abmessungen und den Akkubetrieb ist das Gerät besonders geeignet für mobile Inspektionen.
- znt-Richter – PAC: Diese Plattform verbindet alle am Prozess beteiligten Maschinen und Sensoren. Durch die universelle Schnittstellenkommunikation kann die Plattform prinzipiell jede Maschine in die IT-Landschaft einbinden.
Anwendungsbeispiele
Dampfmaschine
Erstens haben wir eine herkömmliche Dampfmaschine mit Sensorik und Anzeigegerät aufgerüstet (siehe Abb. 1). Dadurch lässt sich eine Fernüberwachung und bedarfsorientierte Instandhaltung realisieren.
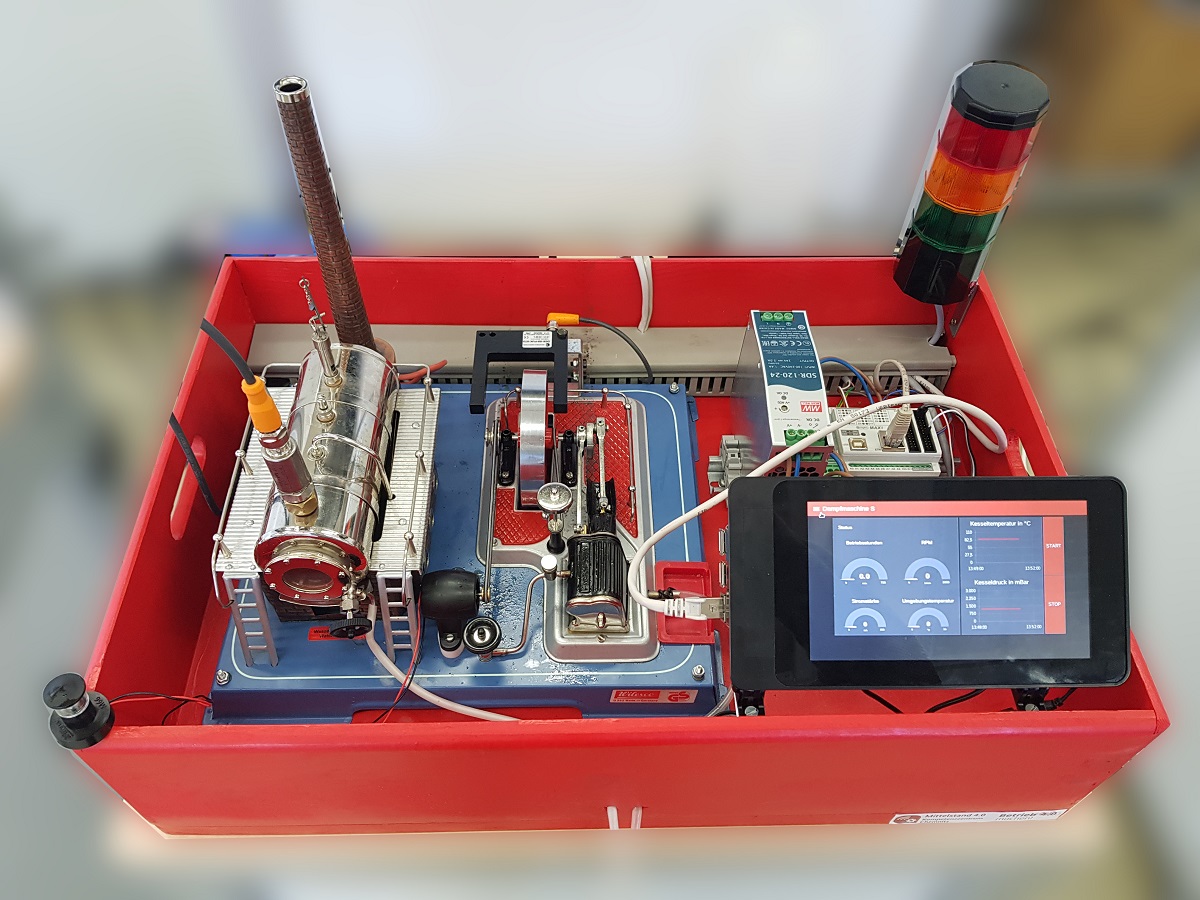
Die verbauten Sensoren (Temperatur, Druck, Drehzahl) ermöglichen eine Schlussfolgerung auf diverse Betriebszustände. Durch Kommunikationsprotokolle wie MQTT/OPC UA lassen sich Informationen, wie bspw. der aktuelle Betriebszustand „Aufheizen“, über das Netzwerk an übergelagerte Systeme weitergeben. Damit ist die Berechnung von Kennzahlen, etwa der Gesamtanlageneffektivität (overall equipment effectiveness – OEE), möglich. In einem Leitstand können somit von einer Person mehrere, ggf. örtlich verteilte Maschinen überwacht werden. So ist ein Besuch der Anlagen vor Ort nur bei Bedarf oder bei Auftreten von Anomalien notwendig.
Die bedarfsorientierte Wartung ist für das Ölungsintervall der Dampfmaschine relevant, da die Lager alle zehn Minuten geölt werden müssen. Um dieses Wartungsintervall zu gewährleisten und eine sichere Instandhaltung zu ermöglichen, wird mittels Lichtschranke ein Drehen des Schwungrades ermittelt, woraufhin die Betriebsminuten gezählt werden. Nach acht Minuten Betriebsdauer schaltet die Heizung der Dampfmaschine selbstständig ab, sodass eine „sichere“ Wartung nach zehn Minuten Betriebsdauer ermöglicht wird. Nach zehn Betriebsminuten erscheint eine Popup-Meldung auf dem Display, die zur Ölung der Lager auffordert.
CNC-Fräse
Zweitens haben wir einen Retrofit mit Hinblick auf prädiktive (voraussagende) Instandhaltung an einer CNC-Fräse durchgeführt. Dazu wurden Schwingungs-, Temperatur- und Drehzahlsensoren an der Maschine angebracht. Diese Sensoren überwachen den Zustand der Maschine und bei Auftreten von Anomalien, die beispielsweise einen überhöhten Werkzeugverschleiß andeuten, kann eine Meldung an das Kontrollzentrum erfolgen. Dadurch ist es möglich in den Prozess frühzeitig einzugreifen, bevor ein Werkzeugbruch auftritt oder Qualitätseinbußen aufgrund von verschlissenem Werkzeug auftreten.
Bandsäge
Drittens haben wir als weiteren Demonstrator eine Bandsäge (siehe Abb. 2) aufgerüstet. Diese wurde mit einer Siemens Logo SPS und einem Einplatinencomputer nachgerüstet. Hierbei war u. a. das Ziel, die Arbeitssicherheit an der Maschine zu erhöhen. Mit Hilfe von Tastern an verschiedenen Serviceklappen der Maschine wird überwacht, ob diese geöffnet werden. Beim Öffnen einer Serviceklappe wird das Sägeband sofort angehalten.
Abb. 2: Smarte Bandsäge zur Erhöhung der Arbeitssicherheit
Diese Beispiele verdeutlichen, wie Retrofit die Arbeitssicherheit oder die Produktivität von Bestandsanlagen erhöht und diese Industrie-4.0-fähig macht. Mit Hilfe unserer Selbstchecks identifizieren Mittelständler spezifische Digitalisierungspotentiale für die eigenen Maschinen und leiten erste Umsetzungs- und Handlungsempfehlungen aus den Ergebnissen ab.
Quellen, Anmerkungen und weiterführende Literatur
- Der Betriebsleiter (2018): Retrofit oder Neuinvestition? Der Betriebsleiter, S. 32-33. ISSN: 0344-5941.