Ein erfolgreiches Prozessmanagement durchführen, bedeutet für Unternehmen, die eigenen Prozesse zu kennen, diese stets im Blick zu halten und kontinuierlich zu verbessern.
In dieser Ausgabe unserer Nachgelesen-Reihe erfahren Sie:
- wie die Durchführung des Prozessmanagements erfolgt,
- welche Arten und Methoden es für die Prozessoptimierung gibt,
- weshalb Digitalisierung erst nach der Prozessoptimierung betrachtet werden sollte und
- wie das Mittelstand 4.0-Kompetenzzentrum Chemnitz die Prozessoptimierung im Workshop durchführt.
Zusammenfassung: Einführung eines Prozessmanagements
Durch den starken industriellen Wandel, hervorgerufen durch globalisierte Märkte, neue Kundenanforderungen, und wachsenden Kostendruck, ist es wichtig, auf neue Situationen schnell und flexibel reagieren zu können. Dies bedeutet auch, seine Unternehmensprozesse zu kennen und einheitlich im Unternehmen zu etablieren, um strategische Ziele effizient und kundennutzenorientiert zu erreichen. Gerade in Zeiten der Wandlungsfähigkeit ist ein stabiles Prozessmanagement wichtig, da dieses sich sowohl an den Geschäftszielen als auch an den Interessen und Anforderungen der Kunden ausrichtet. Deren Hauptaufgaben sind unter anderem:
- die Prozessoptimierung
- die Prozessanalyse
- die Weiterentwicklung von Prozessen
- das Prozesscontrolling
- die Prozesssteuerung
Veränderungen in den Kundenanforderungen können demnach durch ein stabiles Prozessmanagement schnell berücksichtigt werden. Für einen effizienten Einsatz sollte jedoch die Organisationsstruktur eine Prozess- oder eine Matrixorganisation sein.
Die Ein- und Durchführung des Prozessmanagements kann in vier Schritten erfolgen (siehe Abbildung 1). Dabei ist die Implementierung und Durchführung nicht durch eine einzige Person möglich. Für ein stabiles Prozessmanagement braucht es ein Team bestehend aus Projektleitung des Geschäftsprozessmanagements und Prozessberater (bei der Einführung) sowie Prozessmanager, Prozessverantwortlicher, Prozesscontroller und Prozessmitarbeiter (während der Durchführung).
Bevor Schritt vier der Abbildung 1, die Prozessdurchführung, erfolgen kann, müssen alle Unternehmensprozesse identifiziert werden. Hierfür kann der Top-Down-Ansatz oder der Bottom-Up-Ansatz Anwendung finden. In der Praxis hat sich jedoch der Top-Down-Ansatz etabliert. Bei diesem Ansatz muss jedoch beachtet werden, dass nicht nur die Managementebene in den Veränderungsprozess einbezogen wird, sondern jede Unternehmensebene.
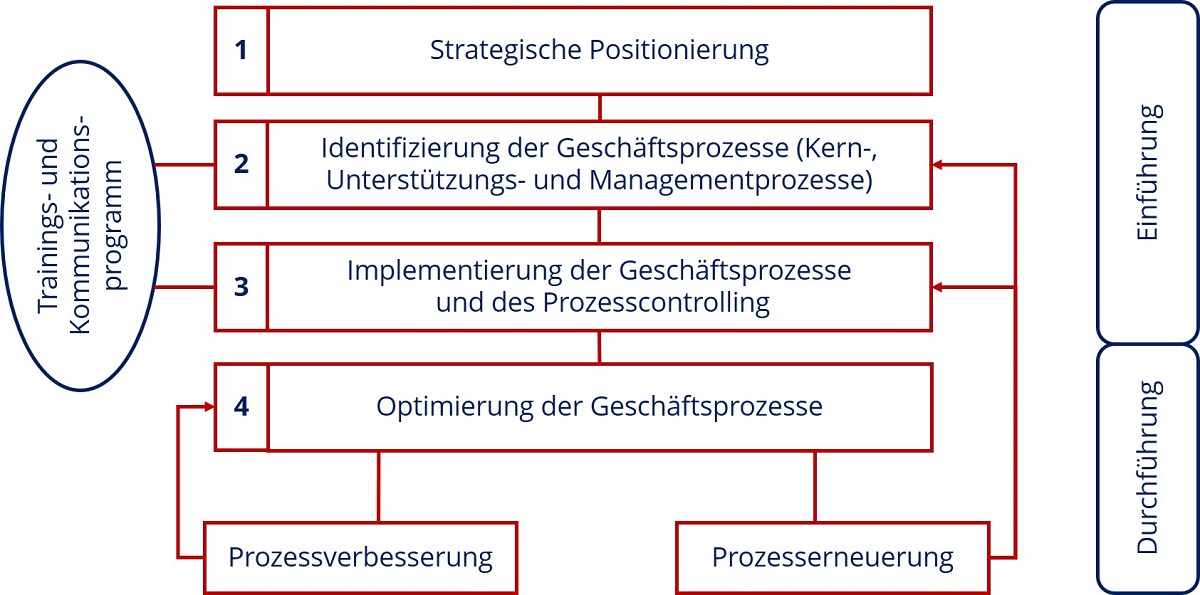
Prozessmanagement durchführen
Nachdem die ersten Schritte zur Einführung des Prozessmanagements abgeschlossen sind, die Rollen und Verantwortungsbereiche sowie die Prozessziele und Rahmenbedingungen festgelegt wurden, das Projektcontrolling implementiert und die Prozesse identifiziert und dokumentiert sind, erfolgt die Durchführung des Prozessmanagements. Hierbei werden die dokumentierten Prozesse hinsichtlich Optimierungspotenziale untersucht und bei Bedarf angepasst. Die Prozessoptimierung unterscheidet zwischen Prozessverbesserung (Evolution) und Prozesserneuerung (Revolution). Beide Maßnahmen haben das Ziel, die Effektivität und Effizienz durch die Optimierung der Geschäftsprozesse zu erhöhen, Kosten zu reduzieren und den Unternehmenswert nachhaltig positiv zu beeinflussen.
Nachdem die Prozesse erfasst und in formalen Modellen beschrieben sind, erfolgt die Prozessoptimierung. Es kann eine radikale als auch eine sanfte Prozessoptimierung Anwendung finden.
Prozesserneuerung
Die radikale Möglichkeit der Prozessoptimierung stellt die Prozesserneuerung, auch Business Process Reengineering (BPR), dar. Diese wurde von Michael Hammer und James Champy in den 1990er Jahren geprägt. Hierbei werden die Geschäftsprozesse fundamental neugestaltet. Ziel ist, die nicht mehr wettbewerbsfähigen Prozesse durch neue, an den Kunden und den neuen strategischen Zielen ausgerichtete Prozesse, zu ersetzen[8]. Diese Methode wird bevorzugt bei der erstmaligen Einführung der Prozessorganisation verwendet, da eine Neuausrichtung des Unternehmens alle strategischen und operativen Unternehmensprozesse maßgeblich beeinflusst. Dieser Veränderungsprozess wird, im Vergleich zur Prozessverbesserung, in der Regel einmalig durchgeführt[4].
Hauptmerkmale von BPR sind:
- Kunden und Prozessfokussierung
- fundamentales Überdenken aller Aufgaben und Aktivitäten
- radikales Redesign aller Strukturen und Verfahrensweisen
- Nutzung von Informationstechnologien
- signifikante Erhöhung der Prozessleistung[6]
Die Anwendung der Prozesserneuerung ist sehr aufwendig und benötigt erhebliche Personalressourcen. Es bedarf intensiver Koordination und unterliegt einem hohen Erfolgsrisiko. Deshalb sollte sich die Prozesserneuerung nur auf strategisch bedeutende Prozesse (Kernprozesse) beziehen, die gleichzeitig gravierende strategische Risiken (unzureichende Kernkompetenzen vorhanden) und Leistungsdefizite (Diskrepanz zwischen Leistungsziel und Leistungsniveau) aufweisen. Trifft dies nicht zu, sollte die Prozessverbesserung Anwendung finden[6].
In den letzten Jahren wurde das BPR jedoch kritisch betrachtet, da ein großer Teil der Prozesserneuerungsprojekte scheiterte. Zurückzuführen ist das auf die fälschliche Fokussierung auf Einzellösungen statt auf den ganzheitlichen Wandel, falsches Führungs- und Kommunikationsverhalten und den Widerstand innerhalb der Organisation. Vor allem der Widerstand ist im Top-Down-Ansatz begründet, da hier die obere Organisationsebene ohne Einbezug der relevanten Prozessmitarbeiter die Systemprozesse radikal erneuert[8].
Dennoch werden Teile der Methode häufig in der Neustrukturierung verwendet, wie
- die Beurteilung und Steuerung der Geschäftsprozesse über nichtfinanzielle Kennzahlen oder
- die abteilungsübergreifende sowie unternehmensübergreifende Definition von Geschäftsprozessen.
Von der radikalen Neugestaltung der Prozesse und der reinen prozessorientierten Gestaltung der Aufbauorganisation wird jedoch Abstand gehalten[4];[6]
Prozessverbesserung
Die sanfte oder auch sukzessive Möglichkeit der Prozessoptimierung stellt die Prozessverbesserung dar.
Das prinzipielle Vorgehen zur Durchführung der Prozessverbesserung ist in Abbildung 2 dargestellt. Dieser Kreislauf orientiert sich an dem von W. Edwards Deming entwickelten PDCA-Zyklus (Plan-Do-Check-Act) auch Deming-Kreis genannt[2];[3].
In Schritt 1 erfolgen eine Prozessanalyse und Bewertung. Hierbei werden die Ist-Prozesse mit den Zielen abgeglichen und die Abweichungen bewertet. Dabei wird beurteilt, wie stark sich das Problem auf die Zielerreichung auswirkt. Ist die Problematik und die Lösung der Abweichung hoch gewichtet, erfolgt in Schritt 2 die Ursachenanalyse, was zu der Abweichung geführt hat. Sind die Ursachen bekannt, wird ein Lösungskonzept im 3. Schritt erarbeitet, welches anschließend in Schritt 4 modelliert und umgesetzt wird. Auf Grundlage des neuen Prozesses erfolgt in Schritt 5 dessen Neubewertung. Hierbei wird geprüft, ob die Prozessverbesserung die gewünschte Wirkung erreicht. Anschließend muss im 6. Schritt die Verbesserung als Standard festgelegt werden, um die alten Fehler und Missstände nicht zu wiederholen. Diese Schritte werden wiederholt, bis das gesetzte Ziel erreicht ist.
Wichtig dabei ist, dass der Zyklus komplett durchgeführt wird. In der Praxis ist häufig eine verkürzte Vorgehensweise verbreitet. Es wird ein Plan für ein Prozessproblem erstellt und gleich umgesetzt, eine tiefere Analyse und Anpassungsmaßnahmen werden nicht berücksichtigt. Wird mit dem Plan das Ziel nicht erreicht, kommt der nächste Plan zum Einsatz. Dieses Vorgehen ist jedoch sehr zeitaufwendig und nicht zielführend im Sinne des PDCA-Zyklus[3].
Zusammenfassend können mit diesen sechs Schritten Schwachstellen im Prozess erkannt und beseitigt werden. Dabei können die Maßnahmen einfach, aber auch sehr umfangreich sein und aus mehreren Einzelmaßnahmen bestehen.
Während einfache Maßnahmen sich schnell durch die Prozessmitarbeiter ändern lassen, sollten aufwendige Prozessveränderungen über ein gesondertes Projekt erarbeitet werden, bei dem die Neuausrichtung und Reorganisation des betroffenen Prozesses erreicht wird[2].
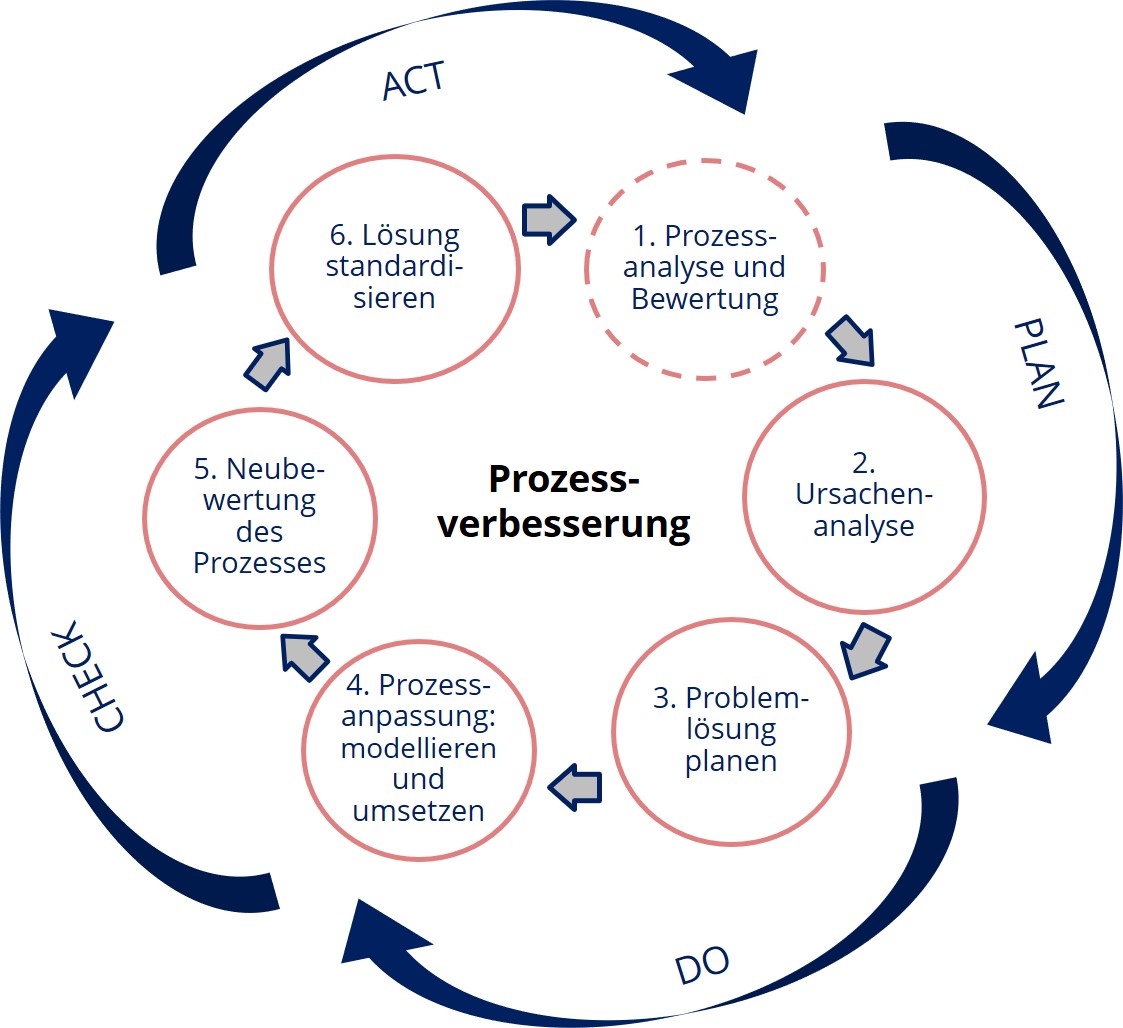
Methoden der Prozessverbesserung
Es gibt verschiedene Methoden für die Prozessverbesserung. Hierzu zählen unter anderem die Total Cycle Time (TCT) , KAIZEN und Six Sigma.
Total Cycle Time (TCT)
TCT zielt darauf ab, die Prozessleistung auf der Ebene der Geschäftsprozesse permanent zu steigern. Hauptaugenmerk ist dabei die Prozesszeit. Diese wird so verkürzt, dass die Qualität und Termintreue gesteigert und die Prozesskosten gesenkt werden.
Wesentliche Kernpunkte sind:
- Ermittlung von Barrieren, die den Prozessablauf behindern
- Beseitigung der Barrieren
- Messen der Wirkung der Barrierenbeseitigung über die Prozesszeit, Termintreue und Prozessqualität
- Vergleich der Messgrößen mit den Zielvorgaben für Prozesszeit, Termintreue und Prozessqualität
Barrieren können hierbei Sachbarrieren, wie fehlende Teile oder Informationen, Prozessbarrieren, wie Doppelarbeit und Wartezeiten sowie Kulturbarrieren, wie unklare Ziele und mangelhafte Kundenorientierung sein[6].
Kaizen
Unter dieser Methode wird eine Philosophie verstanden, die Mitarbeitende befähigt, ihren Arbeitsprozess ständig zu verbessern. Daher wird für KAIZEN auch die Begrifflichkeit „kontinuierlicher Verbesserungsprozess (KVP)“ verwendet. Das Vorgehen orientiert sich hierbei an dem Kreislauf aus Abbildung 2. Die Aufdeckung von Problemen und Fehlern ist gezielt gewollt, da diese Verbesserungen und Fortschritte anstoßen. Es ist gewollt, dass Mitarbeiter Fehler ansprechen, die Verantwortung dafür übernehmen und Maßnahmen zur Behebung vorschlagen, um den Fehler in Zukunft zu vermeiden.
Wesentliche Kernpunkte sind:
- Eliminierung von Verschwendung
- Fokussierung auf Prozesse
- Orientierung an Kunden
- Einbeziehung aller Mitarbeiter
- Teamarbeit
Verschwendung ist dabei alles, was keinen Wert für den Kunden hat, zum Beispiel Überproduktion, Wartezeiten, unnötige Transporte und Tätigkeiten, ungünstige Prozessgestaltung, überhöhte Bestände, fehlerhafte Ergebnisse, Mängel, u. v. m. Es gibt jedoch auch Prozesse, die keinen Wert für den Kunden haben, aber notwendig sind. Diese sind beispielsweise Dokumentationen und Audits.
Ein geeignetes Werkzeug zur Identifizierung nicht werthaltiger Aktivitäten und Verschwendung ist hierbei die Wertstromanalyse. Ebenso Werkzeuge, die von den KAIZEN-Teams genutzt werden sind in Tabelle 1 dargestellt.
Erfolgreiche Anwendung findet diese Methode bei Toyota [1];[3];[6];[8].
Sieben alte Werkzeuge | Sieben neue Werkzeuge | 5-A-Vorgehen (5-S-Methode) | 7-(8)-V-Regeln (Verschwendung vermeiden) |
---|---|---|---|
|
|
|
|
Six Sigma
Eine weitere Methode zur Prozessverbesserung stellt Six Sigma dar. Die Methodik basiert auf Daten, die mit Hilfe von statistischen Mitteln die Prozessstreuung auf ein Minimum reduziert. Sigma ist in der Wahrscheinlichkeitsberechnung die Standardabweichung und bedeutet in der Prozessverbesserung, „dass der Prozess soweit optimiert ist, dass sechs Standardabweichungen in die Toleranz des Prozesses passen“[3]. Ziel ist eine Variation von 6 σ zu erreichen, denn die Varianz gibt mehr Aufschluss über die Leistungsfähigkeit, als die Messung von Durchschnittswerten. Grundvoraussetzung für Six Sigma sind klare Projektaufträge, Ziele, Zeitpläne und Phasenabläufe. Der Einsatz von festgelegten Werkzeugen, die Ermittlung umfangreicher Daten und das systematische Überprüfen von Hypothesen stellen sicher, dass faktenbasierte Entscheidungen und entsprechende Maßnahmen getroffen werden. Der Prozess muss vorhersagbar bzw. beherrschbar sein, denn ein unbeherrschter Prozess ist nur schwer zu verbessern und zu steuern. In dieser Methode findet der DMAIC-Verbesserungszyklus Anwendung, siehe Abbildung 3. Er ist so ähnlich wie der PDCA-Zyklus aufgebaut und besteht aus den Phasen Definieren (Define), Messen (Measure), Analysieren (Analyse), Verbessern (Improve) und Überprüfen (Control)[7].
Bei der Einführung von Six Sigma muss das Management aktiv beteiligt sein und die Stakeholder einbezogen werden, da sie die Leistungen in einer bestimmten Qualität vom Unternehmen erwarten[3];[6].
Es gibt noch weitere Methoden, die bei der Prozessoptimierung Anwendung finden, wie das Total Quality Management, das EFQM-Modell oder das Lean Management. Alle beziehen sich auf das Ziel höchstmögliche Qualität dauerhaft für den Kunden zu erreichen[8].
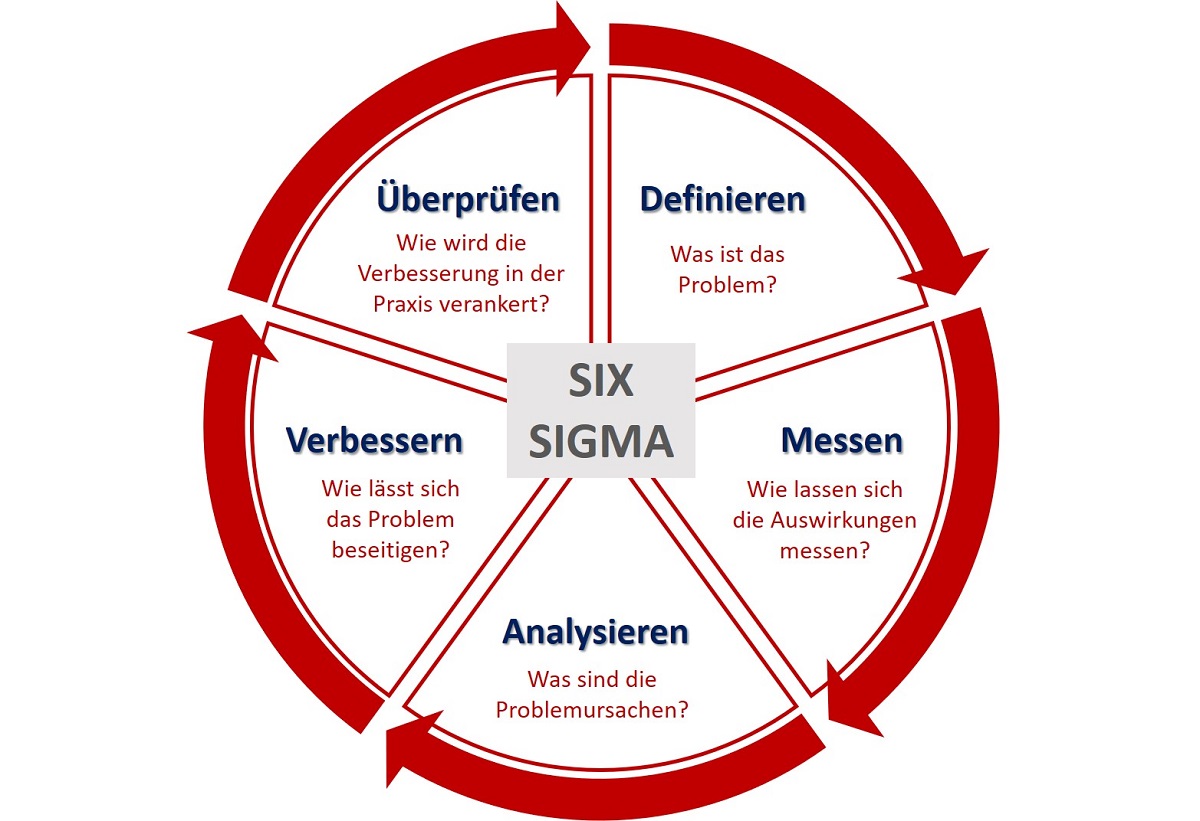
Prozessverbesserung als Grundlage zur Digitalisierung
Gerade bei der Digitalisierung müssen die Prozesse einheitlich, schlank und transparent sein, da sich Fehler auf die Qualität, Kundenzufriedenheit, Durchlaufzeit, Bearbeitungsaufwand und Kosten auswirken. Bevor Sie beispielsweise ein ERP-System einführen, sollten zunächst die Prozesse und Daten bereinigt werden. Wird ein Prozess anders ausgeführt als im System hinterlegt, kann das schwerwiegende Konsequenzen haben. Ebenso verhält es sich mit Daten. Werden veraltete Daten mit digitalisiert, kann dies zu Systemproblemen führen, da die Kapazitäten mit Datenschrott zusätzlich belastet werden.
Im Prozessworkshop des Kompetenzzentrums Chemnitz spielt das Team beispielhaft einen Prozess der Spielzeugautoherstellung von der Kundenbestellung bis zum Versand durch.
Die Teilnehmer nehmen verschiedene Unternehmensrollen ein und modellieren zunächst den Herstellungsprozess. Anschließend wird der Prozess nach dem PDCA-Zyklus analysiert und Verbesserungspotenziale aufgezeigt. Hierbei werden die Prozesse hinsichtlich der in Abbildung 4 aufgezeigten Ansätze, eliminieren, parallelisieren, standardisieren, vereinfachen und verlagern, begutachtet. Dabei wird zunächst untersucht, ob der modellierte Prozess verbessert werden kann, bevor eine Digitalisierung/Automatisierung den Wertschöpfungsprozess verbessert. Ist der Prozess schlank und standardisiert, können unter den gleichen Ansätzen Digitalisierungsmaßnahmen zur weiteren Prozessverbesserung bestimmt werden.
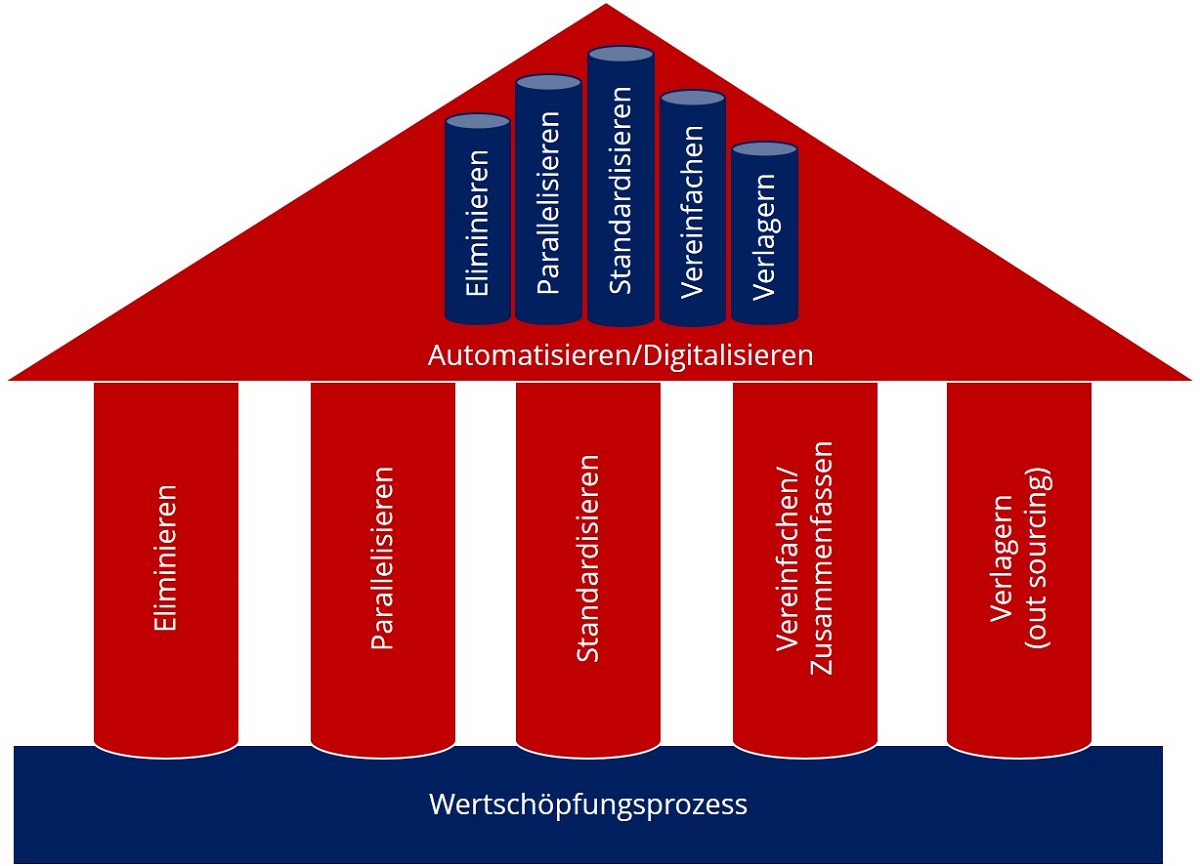
Fazit
Unternehmensprozesse sind vielfältig. Um effizient und wirtschaftlich Erfolg zu haben, sollten Sie die Prozesse transparent, schlank und auf den Kunden sowie auf die strategischen Ziele orientiert ausrichten. Ein stabiles Prozessmanagement hilft dabei, diese Ziele zu erreichen. Ansätze und Methoden zur Prozessverbesserung gibt es viele. Doch gerade für kleine und mittlere Unternehmen kann dies zur Herausforderung werden. Vor allem, wenn das zwingend benötigte Fachwissen über Methoden, Werkzeuge und Ansätze zum Prozessmanagement nicht ausreichend vorhanden ist. Ebenso zwingend erforderlich ist die unternehmensweite Bereitschaft vom einzelnen Prozessmitarbeiter bis hin zur Unternehmensleitung.
Es ist daher empfehlenswert, die Prozessoptimierung mit Hilfe eines externen Beraters und dem kompetenten Fachpersonal unter Einbezug aller Prozessbeteiligter durchzuführen. Vor allem, wenn es um die spezifische Anwendung der aufgeführten Methoden geht. Doch gerade die Möglichkeiten des KAIZEN/KVP können ohne tiefes Fachwissen exemplarisch für einen Unternehmensprozess durchgeführt werden.
Bei beiden Ansätzen der Prozessoptimierung sollte berücksichtigt werden, dass eine reine Erneuerung ohne kontinuierliche Prozessverbesserung eine wesentlich geringere Auswirkung auf die Prozessleistung hat, als mit kontinuierlicher Verbesserung (siehe Abbildung 5)[6].
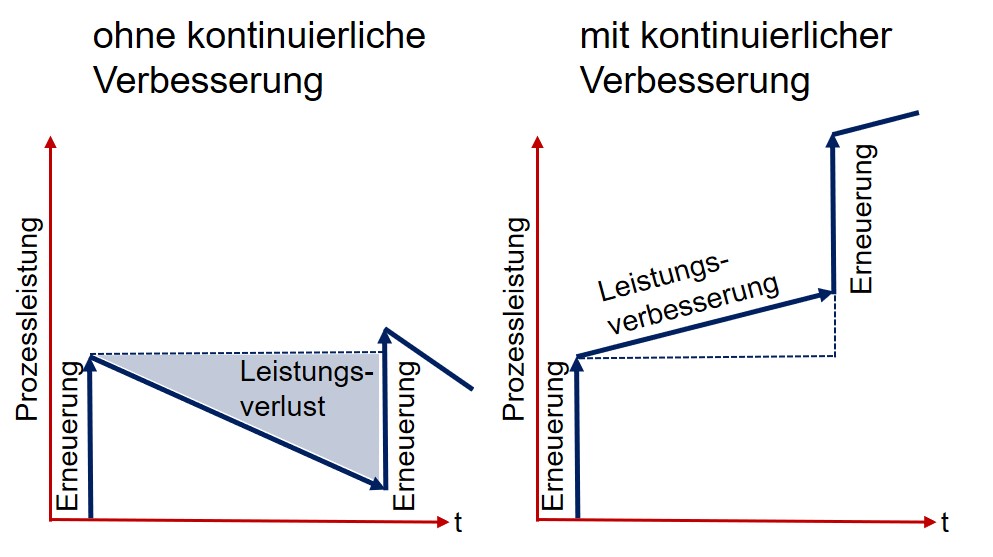
Anmerkungen
Quellen und weiterführende Literatur
- Bertagnolli, F. (2018): Lean Management: Einführung und Vertiefung in die japanische Management-Philosophie. SpringerGabler, Wiesbaden.
- Fleig, J. (2019, 22. Oktober). Prozessmanagement – Prozesse verbessern und optimieren. Abgerufen von https://www.business-wissen.de/hb/prozesse-verbessern-und-optimieren/ [07.04.2020].
- Füermann, T. (2014): Prozessmanagement. Carl Hanser Verlag, München.
- Neumann, S., Probst, C., Wernsmann, C. (2012): Kontinuierliches Prozessmanagement. In J. Becker u. a (Hrsg.), Prozessmanagement – Ein Leitfaden zur prozessorientierten Organisationsgestaltung (S. 303-325). Springer Gabler Verlag, Berlin, Heidelberg.
- REFA Group AG (k. A.). Wertstromanalyse. Abgerufen von https://refa.de/service/refa-lexikon/wertstromanalyse [09.04.2020].
- Schmelzer, H., Sesselmann, W. (2013). Geschäftsprozessmanagement in der Praxis. Carl Hanser Verlag, München.
- Töpfer, A. (2009): Lean Management und Six Sigma: Die wirkungsvolle Kombination von zwei Konzepten für schnelle Prozesse und fehlerfreie Qualität. In A. Töpfer (Hrsg.) Lean Six Sigma: Erfolgreiche Kombinationen von Lean Management, Six Sigma und Design for Six Sigma (S. 25-68). Springer Verlag, Berlin, Heidelberg.
- Zeidler, S. (2010, 08. Juni). Prozesse – Top 5 Methoden der Prozessoptimierung. Abgerufen von https://www.gruenderszene.de/operations/die-top-5-methoden-der-prozessoptimierung [07.04.2020].